rorypoole
Veteran Member
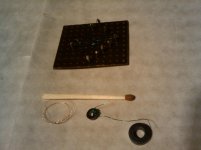


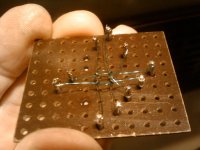
the 4 bit core memory is built on a very old brown pcb at the top of the pic, the larger toroid is the same type as one core memory builder I found online, Wayne used the toroid to build a 1 bit core memory but I thought a smaller core of the same type would work better, I do not know much about toroid core types, but the one used on the site may not be ideal? a smaller toroid should pass the tiny spike with less attenuation, but I will test both.
I will only need 3 or 4 wires per core, the 4 bit core was made as a test so I could see if I could thread the cores in the wright shape, also so could electrically test the cores under different conditions so I know its tolerances.
I am getting a microscope for the 0.5mm cores!
Last edited: