TJ_Mossman
Experienced Member
Hi All,
I've had a 2nd TU56 arrive the other week, and I've just got around to giving it an initial look-over before I start refurbishing it.
One thing that was immediately apparent is that all but one of the drive motors had seized up. After getting them out I could see that at some point the bushings had dried out and stuck to the shaft, and that the springs had been bent and snapped. They were really stuck on hard and unfortunately got scored by the shaft on the way out as the set screws for the hubs had roughed them up. (I'll probably have to lightly sand it back down before I replace them)
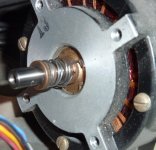
Has anyone gone about replacing these? (P/N 12-9926 for the bushings and 12-9917 for the spring)
I see that they're not normal Oilite bushings and springs. The bushings measure ID=8mm, OD=10mm, Flange Diameter=12mm, Flange Length=2mm Length=6mm (total), and have a small hole to retain the spring. The spring has an internal diameter of 10mm and is about 25mm long. One end is bent inwards trap the bushing, and the other end is bent outwards to trap the C-ring on the motor.
I might be able to make the springs myself by finding a similar one and bending it, but I haven't had any luck finding bushings the right size, and lack the tools needed to machine them without damage.
Meanwhile I've stripped down the motors and re-lubricated them. They use standard GMN 608 bearings, just like skateboards.
I suppose I'll move onto the PSU next. As with my other unit, a bunch of wires got burned by one of the dropper resistors. I'm tempted to find some high-temperature cloth coated wire to replace it with, rather than repeating my last kludge where I just put a few layers of heat-shrink over the existing wires.
I've had a 2nd TU56 arrive the other week, and I've just got around to giving it an initial look-over before I start refurbishing it.
One thing that was immediately apparent is that all but one of the drive motors had seized up. After getting them out I could see that at some point the bushings had dried out and stuck to the shaft, and that the springs had been bent and snapped. They were really stuck on hard and unfortunately got scored by the shaft on the way out as the set screws for the hubs had roughed them up. (I'll probably have to lightly sand it back down before I replace them)
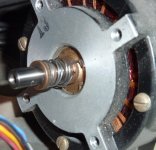
Has anyone gone about replacing these? (P/N 12-9926 for the bushings and 12-9917 for the spring)
I see that they're not normal Oilite bushings and springs. The bushings measure ID=8mm, OD=10mm, Flange Diameter=12mm, Flange Length=2mm Length=6mm (total), and have a small hole to retain the spring. The spring has an internal diameter of 10mm and is about 25mm long. One end is bent inwards trap the bushing, and the other end is bent outwards to trap the C-ring on the motor.
I might be able to make the springs myself by finding a similar one and bending it, but I haven't had any luck finding bushings the right size, and lack the tools needed to machine them without damage.
Meanwhile I've stripped down the motors and re-lubricated them. They use standard GMN 608 bearings, just like skateboards.
I suppose I'll move onto the PSU next. As with my other unit, a bunch of wires got burned by one of the dropper resistors. I'm tempted to find some high-temperature cloth coated wire to replace it with, rather than repeating my last kludge where I just put a few layers of heat-shrink over the existing wires.