Hi all
I have an XT clone with a Transteque HC-101 A1 controller card and a MiniScribe 8438 hard disk. It was working fine a few weeks ago but now it spins up and a moment later down again, then flashes an error code:
stason.org
According to this it's "Code 4 - Index pulse not detected during spinup", if I got this right?
Where do I start? I reseated the ICs on the controller and tried different slots, but the problem is probably the drive itself, right? I also didn't find any documentation about the controller card... I hope it'll be fine.
Thanks for any hints!
I have an XT clone with a Transteque HC-101 A1 controller card and a MiniScribe 8438 hard disk. It was working fine a few weeks ago but now it spins up and a moment later down again, then flashes an error code:
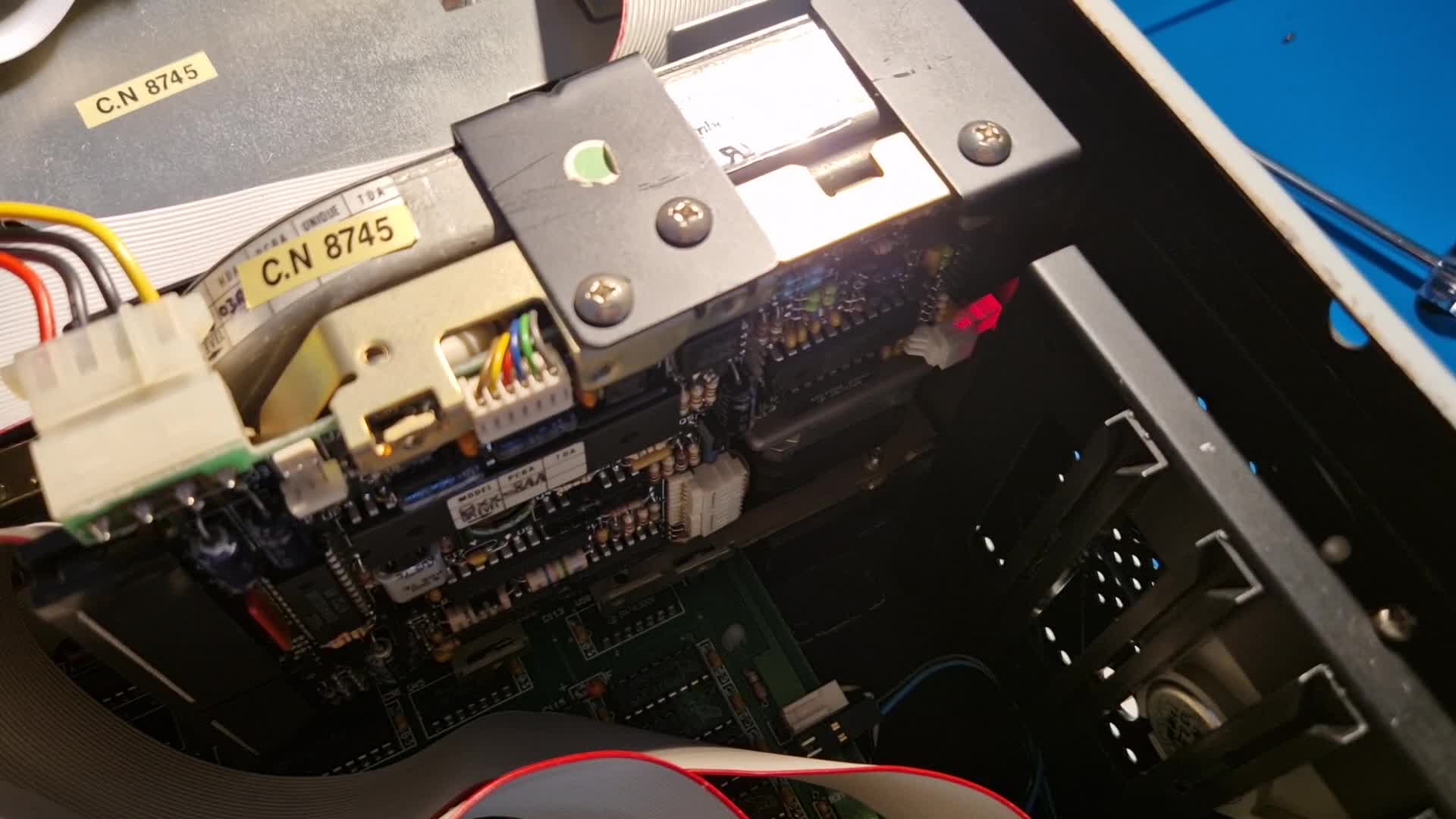

Hard Drive: MINISCRIBE: M8438F 33MB 3.5"/HH RLL ST412
Manufacturer: MINISCRIBE model: M8438F capacity: 33MB, physical size: 3.5in/HH , interface: RLL ST412 , hard driver specs and jumper settings, layout and features
According to this it's "Code 4 - Index pulse not detected during spinup", if I got this right?
Where do I start? I reseated the ICs on the controller and tried different slots, but the problem is probably the drive itself, right? I also didn't find any documentation about the controller card... I hope it'll be fine.
Thanks for any hints!