Dear Forum Members,
This is a continuation post regarding my previous post about the required dummy load resistor.
With my dummy load resistor, I am still getting the same in-circuit measured results when trouble shooting (PDF page 31, 2-1 THE SWITCHING REGULATOR UNIT FAILURE) as without any load.
Here's the specs for the required resistor network from the service manual:
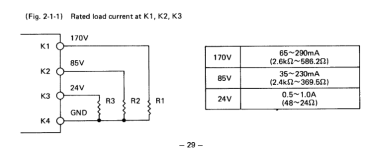
My dummy load resistor is
K1 -> K4: AX9W 820R + AX9W 820R
K2 -> K4: ROYAL 162 P 5W 2K2 J
K3 -> K4: 10W22OhmJ + 10W22OhmJ
With the dummy load resistor connected to, the measured resistances are
K1 -> K4: 1.558k
K2 -> K4: 2k
K3 -> K4: 44 Ohm
and for comparison, with the MAIN PWB connected:
K1 -> K4: 47.8k
K2 -> K4: 46.1k
K3 -> K4: 879 Ohm
and here's a recap of some in-circuit, trouble shooting flow related measurements:
This is a continuation post regarding my previous post about the required dummy load resistor.
With my dummy load resistor, I am still getting the same in-circuit measured results when trouble shooting (PDF page 31, 2-1 THE SWITCHING REGULATOR UNIT FAILURE) as without any load.
Here's the specs for the required resistor network from the service manual:
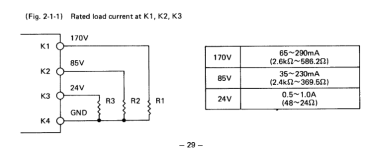
My dummy load resistor is
K1 -> K4: AX9W 820R + AX9W 820R
K2 -> K4: ROYAL 162 P 5W 2K2 J
K3 -> K4: 10W22OhmJ + 10W22OhmJ
With the dummy load resistor connected to, the measured resistances are
K1 -> K4: 1.558k
K2 -> K4: 2k
K3 -> K4: 44 Ohm
and for comparison, with the MAIN PWB connected:
K1 -> K4: 47.8k
K2 -> K4: 46.1k
K3 -> K4: 879 Ohm
and here's a recap of some in-circuit, trouble shooting flow related measurements:
- 0V across any combination between K4-K1
- Steady +17V across pins 13 and 16 of IC601.
- Voltage across + and - terminals of D601 is +325V (no mention in the service manual what this should be, with my input 230VAC this is OK? RMS?)
- R603 should be OK (~68k in-circuit)
- R630 should be OK (~47k in-circuit)
- R610 should be OK (~0.4 in-circuit)
- R616 and R617 should be OK (6.9 in-circuit)
- Fuse F601 is OK.
- R624 should be OK (~69 in-circuit)
- R627 should be OK (2,2 in circuit)
- R601 should be OK (~15 in-circuit)