Hi all,
I am trying to repair a 12-inch monochrome (green) CRT monitor, Daewoo DM-120MWA, which was made in the 80s for 8-bit computers.
When I got it, it did not work at all. Perhaps somebody might have tried to fix it in the past, I guess. I am a hobbyist without any occasion to learn electronics properly. Actually, I had no background about CRT circuits, so I read some very useful information on CRT repair on the web, but I think I still don't have full understanding. So what I could do so far (see below) was limited and not enough to repair it, or to figure out exactly what part is problematic. (Need help please!)
The problem. When the monitor is turned on, a resistor (R618 in the left hand side of the schematics below) between the power supply and FBT gets very hot quickly, and eventually burns.
I could not find a schematic or service manual on the web, so I drew part of the circuits on my own (see below). It includes the power supply, horizontal and vertical circuit, but the video/audio parts are not yet drawn. I hope this is enough, because I guess the problem is in the horizontal circuit.
Partial Schematics.
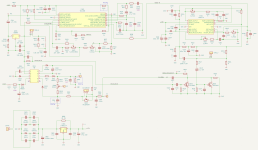
The original R618 was 4.7 ohm, 0.5W (9mm long). A replacement R618 luckly lasts for 2 seconds at least, so I could turn on the monitor and quickly perform some measurements (and then turn it off) before it burns.
I meaured the current through R618 with a DMM. It was about 2A. So it was way higher than what R618 can endure.
I thought that the reason might be that the horizontal output resistor (Q601 BU806, right?) was controlling the current into FBT correctly. So I measured the voltage of the base and collector of Q601. The waveforms are as follows.
Q601 base waveform
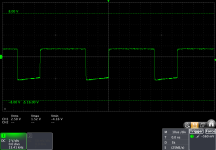
Q601 collector waveform
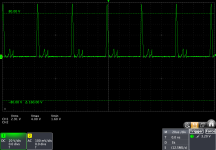
I thought that the collector output was problematic. But I could not figure out exactly which part is malfunctioning. Initially, I thought the horizontal output transistor could be the problem. So I replaced Q601 with a new BU608, but the waveforms were the same. So, perhaps Q601 is not why it does not work.
I checked the caps C613 and C614 (I guesses that they are "safety" capacitors... right?). Their values (measured by an DMM after desoldering) look okay.
I also checked the values of caps around the horizontal yoke and FBT: C611, C612, C615, C616, C902. The values look okay. I didn't check other electrolyte caps yet, but at eye inspection, all of them look okay. I also checked D602, D601. Both looked okay.
One thing I noticed was that C901, a cap in the FBT part, was missing on the PCB. I guess C901 was removed by somebody, looking at the remaing solder marks. (R621 and R911 in the schematics are also missing on the PCB, but it is likely that it was originally missing.)
The power supply part works well, I believe. It produces +12V steadily, even when R618 gets very hot.
What could I do from here? Any help and comments will be greatly appreciated!!!
FYI, I attach photos of the PCB.
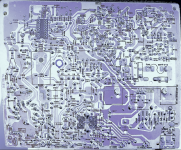
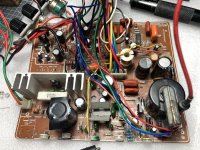
I am trying to repair a 12-inch monochrome (green) CRT monitor, Daewoo DM-120MWA, which was made in the 80s for 8-bit computers.
When I got it, it did not work at all. Perhaps somebody might have tried to fix it in the past, I guess. I am a hobbyist without any occasion to learn electronics properly. Actually, I had no background about CRT circuits, so I read some very useful information on CRT repair on the web, but I think I still don't have full understanding. So what I could do so far (see below) was limited and not enough to repair it, or to figure out exactly what part is problematic. (Need help please!)
The problem. When the monitor is turned on, a resistor (R618 in the left hand side of the schematics below) between the power supply and FBT gets very hot quickly, and eventually burns.
I could not find a schematic or service manual on the web, so I drew part of the circuits on my own (see below). It includes the power supply, horizontal and vertical circuit, but the video/audio parts are not yet drawn. I hope this is enough, because I guess the problem is in the horizontal circuit.
Partial Schematics.
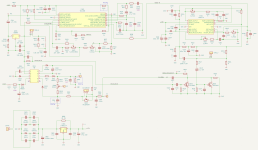
The original R618 was 4.7 ohm, 0.5W (9mm long). A replacement R618 luckly lasts for 2 seconds at least, so I could turn on the monitor and quickly perform some measurements (and then turn it off) before it burns.
I meaured the current through R618 with a DMM. It was about 2A. So it was way higher than what R618 can endure.
I thought that the reason might be that the horizontal output resistor (Q601 BU806, right?) was controlling the current into FBT correctly. So I measured the voltage of the base and collector of Q601. The waveforms are as follows.
Q601 base waveform
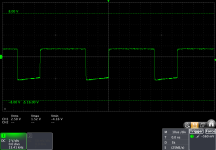
Q601 collector waveform
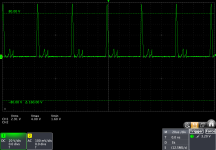
I thought that the collector output was problematic. But I could not figure out exactly which part is malfunctioning. Initially, I thought the horizontal output transistor could be the problem. So I replaced Q601 with a new BU608, but the waveforms were the same. So, perhaps Q601 is not why it does not work.
I checked the caps C613 and C614 (I guesses that they are "safety" capacitors... right?). Their values (measured by an DMM after desoldering) look okay.
I also checked the values of caps around the horizontal yoke and FBT: C611, C612, C615, C616, C902. The values look okay. I didn't check other electrolyte caps yet, but at eye inspection, all of them look okay. I also checked D602, D601. Both looked okay.
One thing I noticed was that C901, a cap in the FBT part, was missing on the PCB. I guess C901 was removed by somebody, looking at the remaing solder marks. (R621 and R911 in the schematics are also missing on the PCB, but it is likely that it was originally missing.)
The power supply part works well, I believe. It produces +12V steadily, even when R618 gets very hot.
What could I do from here? Any help and comments will be greatly appreciated!!!
FYI, I attach photos of the PCB.
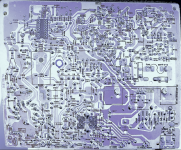
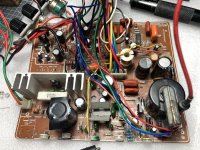
Last edited: