falter
Veteran Member
This isn't specifically a vintage computer thing but, if you're into vintage computers in a big way you're going to eventually run into a need for some kind of desoldering tool. Desoldering is something I absolutely hate. I'm not good with it, I frequently damage things in the process, and it just takes forever. Previous to today, I had been using those (not too cheap) Radio Shack blue and white plastic solder suckers. These are adequate for a little while, but the plastic nozzles are easily melted and deformed. And at $12 a pop (before The Source, our Radio Shack replacement closed).. they were getting a bit expensive.
I'm sure part of the issue is not the tool but the idiot handling it (me), but in reading around I find desoldering is definitely a chore few look forward to. Anyway, I went looking for a better mousetrap and settled on one of these Japanese 'engineered' solder suckers, and thought I'd share my experience with those who like me may not have much experience with this stuff.
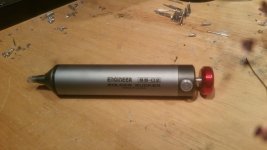
Okay, so they definitely put the 'engineer'ing into this thing. It costs $20.00 or so USD and it definitely feels like it should be. It is basically a solid piece of metal. The pushrod mechanism is very well built and strong. In fact, after a few desolderings, I had to take a break because it really tested the muscle in my thumb. Being metal through and through, the concern would obviously be solder getting stuck to the insides. The idea, as far as I can ascertain, is that there is a small silicone tube attached to the end. These take the brunt of the heat from the iron much better than plastic. I did about 30 desoldering operations and where my cheapo RS unit would have already been starting to get shaggy around the tip, this totally shrugged it off. As I mentioned, the suction is quite good. If you can get it right over what you're soldering it'll pull the solder right out of there, presto changeo. However, if you're not careful and going too fast, the thing can actually do the reverse and blow hot solder onto your skin! Anyway, the overall concept seems solid.
However.
I might be dense, but the silicone tube doesn't make much sense. The pushrod/piston/pin/whatever it's called doesn't extend much more than maybe 1/8th of an inch out of the end of the steel nozzle. You can't really make the tube longer than that.. otherwise solder just gets stuck in there. Where my RS units would take a big honking gob of solder with ease, this thing can only handle little nuggets, as much as can fit in about 1/8th an inch of silicone tube. As delivered the unit comes with a tube attached that is three times that length - solder simply gets stuck up in there. It also comes with some spare tubing to replace the tip as it wears out. It's quite possible there's something I'm doing wrong, of course. But I don't think so. As I mentioned, the suction is very strong - a few times it sucked the solder way past the tube and into the body of the unit itself, which is a problem.. because the solder sticks to the metal inside and requires Herculean force to dislodge. And I found because I couldn't cut the tube evenly, it was a bit tricky getting it positioned in such a way to get maximum suction on the solder.
So is it worth it? Well, I think it did save me quite a bit of time. I've been desoldering my first TVT boards (because I made them too small) and it is a painful and arduous task with my RS unit. With this guy, it's still a bit of a pain because of the limited amount it can handle, but it does really pull a lot more solder off. I probably got the job done in about half the time vs the cheap RS unit. It does come at a cost of tiring out your hand more quickly though. I give it an A on overall quality, a C+ on functionality, for a B grade overall. To get to an A, they'd need to figure out a way to get the tube a bit longer for more capacity.. probably wtih a longer pin to push all the way through it. This would be useful in situations where you're taking on significant amounts of solder. Maybe they could teflon it inside the barrel to help solder that gets stuck up in there free more easily? I'm not sure. Like I said, I may be using it wrong. The instructions are in Japanese which makes it a bit of a challenge. But I think I'm using it correctly.
Anyway, not a bad buy. Not a great one either, but not bad.
I'm sure part of the issue is not the tool but the idiot handling it (me), but in reading around I find desoldering is definitely a chore few look forward to. Anyway, I went looking for a better mousetrap and settled on one of these Japanese 'engineered' solder suckers, and thought I'd share my experience with those who like me may not have much experience with this stuff.
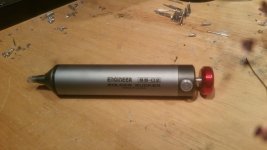
Okay, so they definitely put the 'engineer'ing into this thing. It costs $20.00 or so USD and it definitely feels like it should be. It is basically a solid piece of metal. The pushrod mechanism is very well built and strong. In fact, after a few desolderings, I had to take a break because it really tested the muscle in my thumb. Being metal through and through, the concern would obviously be solder getting stuck to the insides. The idea, as far as I can ascertain, is that there is a small silicone tube attached to the end. These take the brunt of the heat from the iron much better than plastic. I did about 30 desoldering operations and where my cheapo RS unit would have already been starting to get shaggy around the tip, this totally shrugged it off. As I mentioned, the suction is quite good. If you can get it right over what you're soldering it'll pull the solder right out of there, presto changeo. However, if you're not careful and going too fast, the thing can actually do the reverse and blow hot solder onto your skin! Anyway, the overall concept seems solid.
However.
I might be dense, but the silicone tube doesn't make much sense. The pushrod/piston/pin/whatever it's called doesn't extend much more than maybe 1/8th of an inch out of the end of the steel nozzle. You can't really make the tube longer than that.. otherwise solder just gets stuck in there. Where my RS units would take a big honking gob of solder with ease, this thing can only handle little nuggets, as much as can fit in about 1/8th an inch of silicone tube. As delivered the unit comes with a tube attached that is three times that length - solder simply gets stuck up in there. It also comes with some spare tubing to replace the tip as it wears out. It's quite possible there's something I'm doing wrong, of course. But I don't think so. As I mentioned, the suction is very strong - a few times it sucked the solder way past the tube and into the body of the unit itself, which is a problem.. because the solder sticks to the metal inside and requires Herculean force to dislodge. And I found because I couldn't cut the tube evenly, it was a bit tricky getting it positioned in such a way to get maximum suction on the solder.
So is it worth it? Well, I think it did save me quite a bit of time. I've been desoldering my first TVT boards (because I made them too small) and it is a painful and arduous task with my RS unit. With this guy, it's still a bit of a pain because of the limited amount it can handle, but it does really pull a lot more solder off. I probably got the job done in about half the time vs the cheap RS unit. It does come at a cost of tiring out your hand more quickly though. I give it an A on overall quality, a C+ on functionality, for a B grade overall. To get to an A, they'd need to figure out a way to get the tube a bit longer for more capacity.. probably wtih a longer pin to push all the way through it. This would be useful in situations where you're taking on significant amounts of solder. Maybe they could teflon it inside the barrel to help solder that gets stuck up in there free more easily? I'm not sure. Like I said, I may be using it wrong. The instructions are in Japanese which makes it a bit of a challenge. But I think I'm using it correctly.
Anyway, not a bad buy. Not a great one either, but not bad.
Last edited: