I've been trying to bring some order out of the chaos. I have finished one of my quad card storage solutions and here are some more photos.
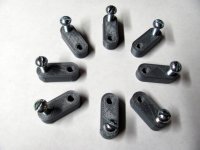
These are what I ended up with to join the blocks that hold the cards. I tried 3D printing the threads but at 8-32 size the threads are not really there. With these I printed the parts with the correct size hole so that I could run a tap through them. They hold very well. The 8-32 screws are from a box of 100 I must have purchased 40 years ago. Period correct screws?
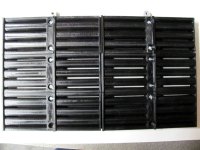
This is three of the blocks connected by the joiners. Each of the blocks takes a little over 4 hours to 3D print. I need 7 for each storage box.
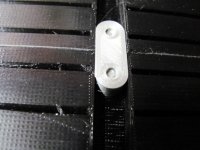
This is a closeup of the joiner in action.
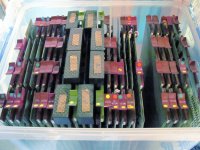
Here is the first box loaded up with cards. The left most cards up to and including the M8320 are the boards that will probably end up in the 8/e. The other cards are extra CPU cards some of which are known to need fixing. This is about half of the quad cards in my collection. There is a working EAE in the cards on the left. There are two 8k core memory sets so hopefully I will have a working 16k in this box.
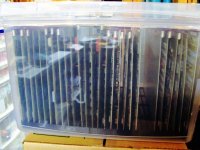
Here is a side view of the "Bankers Box" holding the cards.
Overall I am pretty happy with the way this turned out. I am going to make 7 more blocks to fill a second box and then figure out a hex board solution. These boxes are large enough to hold hex boards in the other orientation.
There were 8 more boards in the DECset 8k than what I am going to put back in it for now. There was a DK8EP (M518 and M860) Real time clock, a KP8E (M849) which is the power fail auto restart module, an M8350 which is a Posibus interface, two M1703s and a M1705 module which are 12 bit interface cards. There was also an unknown card made by someone other than DEC. It might have been the interface to the typesetter. I will post a photo of that later.
I cleaned up a little more of my bench in order to make room for the above mentioned 8/e. While I know the CPU cards work (We tested them in Vince's 8/e) I don't know about anything else that was in the chassis.